The process of CNC machining involves the usage of a computer system to regulate equipment tools for a more consistent and trusted output. Specialized methods and devices are commonly used to maximize the machining procedure, which can include using cutting tools coated with hard materials to reduce wear and enhance performance when working with soft metals like copper.
Discover copper cnc machining exactly how copper CNC machining combines sophisticated modern technology with lasting techniques to generate detailed, high-precision parts, driving technology throughout sectors such as electronic devices, auto, and aerospace.
Among the primary advantages of CNC machining copper is the capability to generate intricate forms that standard machining techniques may not accommodate. The repeatability of the CNC machining process makes certain that mass manufacturing of copper components preserves uniformity, thus fulfilling rigorous sector requirements.
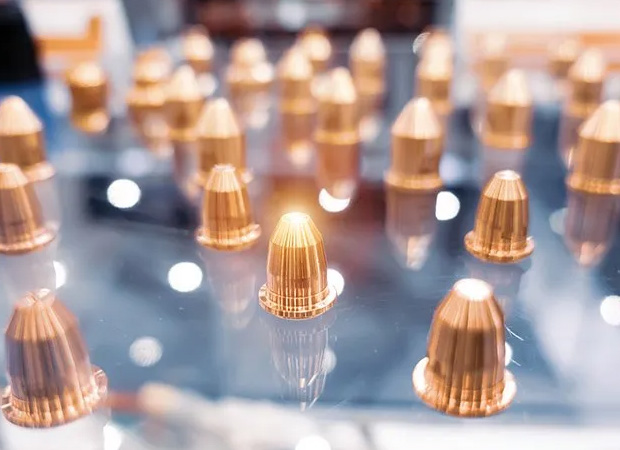
Temperature administration plays a crucial function in the CNC machining of copper due to its ability to carry out heat quickly. High-speed machining can lead to significant warm generation, which might negatively influence the homes of the copper and exacerbate tool wear.
The sustainability element of CNC machining copper is not to be overlooked. CNC machining, combined with lasting practices, can reduce waste by permitting manufacturers to use scrap copper from various other processes.
Along with sustainability, cost-effectiveness is an additional important element for suppliers choosing CNC machining for copper parts. Though the preliminary financial investment in CNC machinery might be substantial, the long-lasting advantages can outweigh the prices. CNC machining gives a reduction in labor expenses as a result of its computerized nature and diminishes the requirement for considerable manual intervention. The exact control & repeatability supplied by CNC technology reduces scrap rates, reducing material costs. Additionally, for small to medium batch manufacturing runs, CNC machining can verify a lot more affordable contrasted to traditional machining processes, as it allows for seamless modifications and style adjustments without considerable retooling. This ability to pivot quickly can be beneficial, especially in busy sectors where market needs can shift unexpectedly.
As technology progresses, the performances within CNC systems are expanding, better boosting the abilities of copper machining. These simulations allow better planning of device courses and elucidate how the copper product will certainly respond throughout the machining process.
Knowledgeable machinists should be experienced in translating design specs, selecting the proper tools, and changing machining criteria to reduce concerns connected with copper's one-of-a-kind machining qualities. Crossbreed machining, which integrates typical CNC machining methods with additive production, is emerging as a feasible method for creating intricate copper parts, blending the toughness of both technologies and possibly revolutionizing just how manufacturers come close to copper production.
In the world of r & d, CNC machining is aiding the expedition of new copper alloys to improve efficiency additionally. By manufacturing copper with products such as nickel, tin, or light weight aluminum, producers can craft compounds that have enhanced toughness, electrical performance, and resistance to put on and corrosion. These advancements can result in arising applications in sectors that depend greatly on conductive products, such as renewable resource and electrical vehicles. Additionally, as international industries function towards greater energy performance, copper's role as a conductor in electronic circuits will certainly continue to be paramount, driving demand for innovative machining solutions.
The aerospace and auto sectors are additionally eager adopters of copper CNC machining, specifically where light-weight parts are of essential importance. As the shift towards electrical and hybrid lorries proceeds, the need for high-performance copper elements will likely rise, therefore propelling the need for innovative CNC machining techniques that make certain performance and top quality in manufacturing.
As CNC machining innovation continues to develop, it allows for further automation, where basic procedures such as device adjustments, assessments, and upkeep can be set right into the manufacturing cycle. This development implies that producers will be able to achieve higher productivity levels, much shorter preparations, and better adaptability in suiting custom-made demands or variations in style. Consequently, businesses that participate in CNC machining procedures are much better matched to pivot in feedback to the changes in consumer and market demands, fostering growth in a significantly affordable landscape.
Discover countersink size chart exactly how copper CNC machining combines sophisticated innovation with sustainable techniques to generate elaborate, high-precision components, driving innovation throughout markets like electronic devices, vehicle, and aerospace.
The worldwide market for CNC machining of copper is seeing significant development, affected by aspects such as the increase of smart technologies, electrical automobiles, and continuous efforts to boost power effectiveness across various applications. It mirrors an assembling trend where businesses welcome digital manufacturing techniques, assisting shape the future of manufacturing. Developing collaborations with suppliers, technology carriers, and academic community can improve access to the current technologies and understanding within the field, cultivating a collaborative setting that drives forward-thinking efforts. In this skill, training and evolution growth stay paramount; buying workforce education and learning on CNC machining methods, developments, and product sciences will certainly equip manufacturers to remain ahead of the contour.
As markets advance and the borders of technology expand, accepting CNC machining's capacity will certainly be vital to realizing unprecedented growth and advancement in the use of copper items. The harmony of copper's material homes with sophisticated CNC machining strategies proclaims a new age in which accuracy, sustainability, and performance job together to develop revolutionary components that will define the future of production and beyond.